Kinetic project team members
- Shuainan Yang
- Shinnosuke Komiya
- Shirley Wu
Last week we left off with the idea of a candle to a steam engine powering an LED and had ordered the cheapest and most minimal steam engine we could find because we didn't want to build it from scratch.
Turns out, it was a stirling engine, which is conceptually a little different in that it works based on a temperature differencial between the top and bottom plate moving the piston, rather than pressure built up from steam moving the piston.
Unfortunately the stirling engine was really delicate and we couldn't extract any work from it (the right video above is us trying to put a rubber band on the wheel to use it to drive a motor, which failed).
So we decided to build it from scratch lol.
After watching a whole bunch of videos on Youtube, we determined that the must-haves for a steam engine were:
- a candle for fire
- a water vessel that can withstand fire, boiling temperatures and steam
- a syringe to act as a piston
- a lightweight flywheel
That lightweight flywheel would then get connected to a motor that would power an LED.
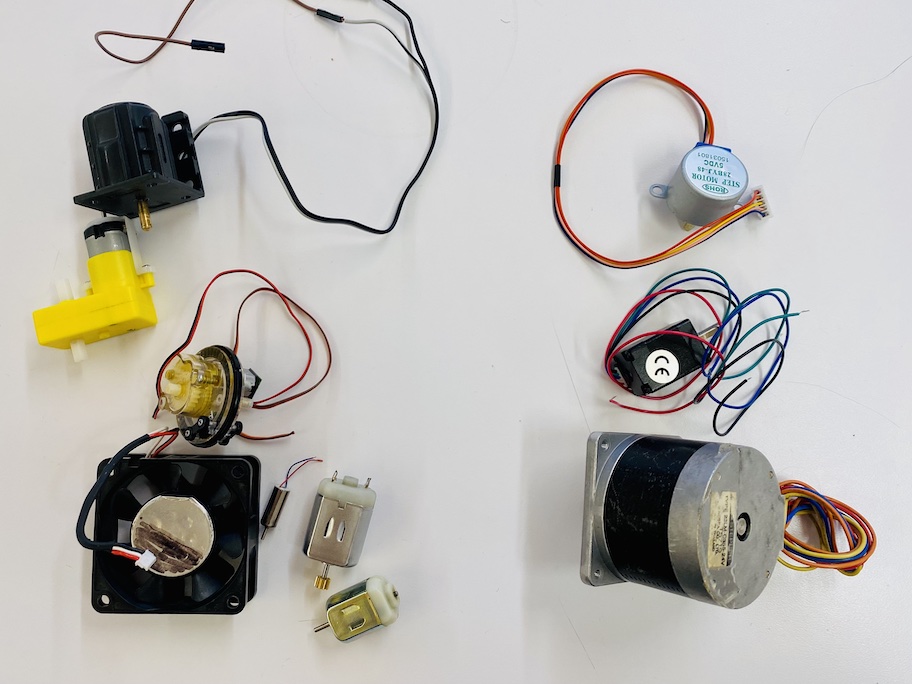
With the video knowledge in mind, we set out to acquire some copper tubing (husband's suggestion!) as a more reusable water vessel than the drink cans the Youtube videos used.
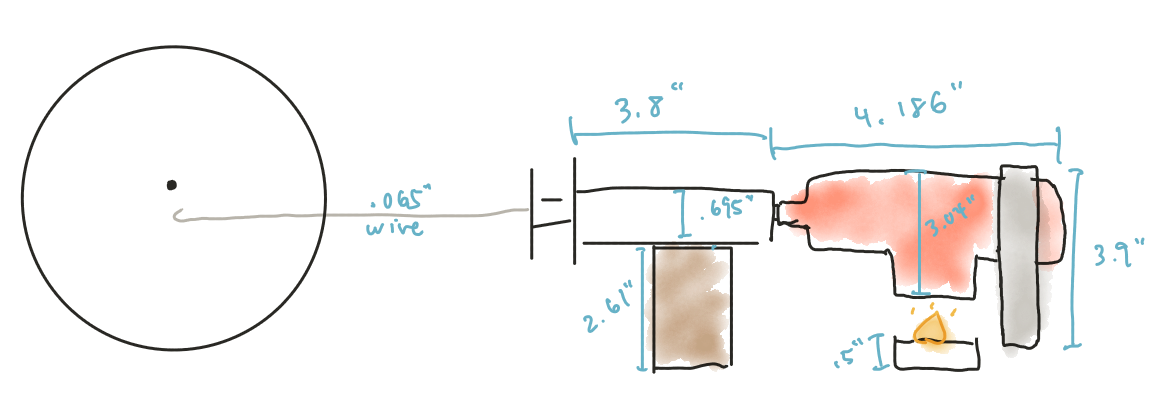
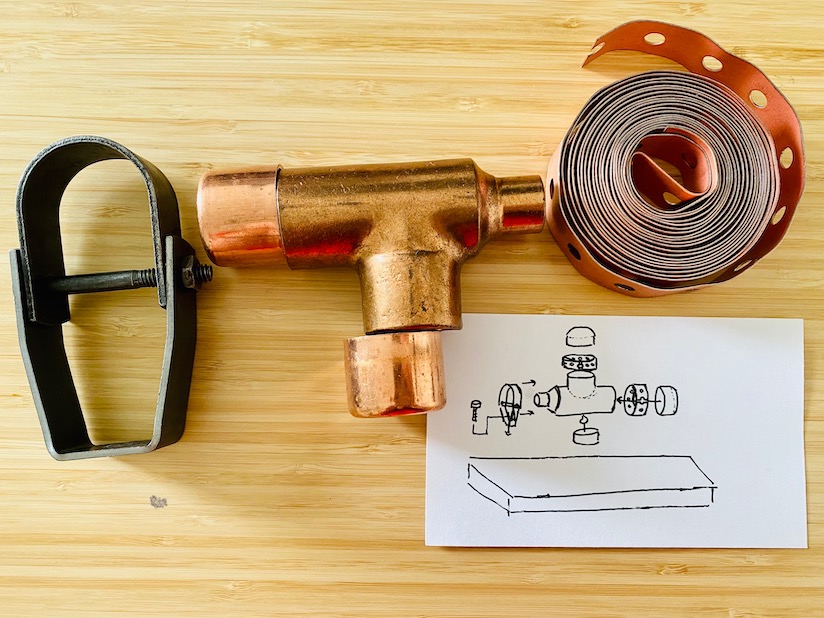
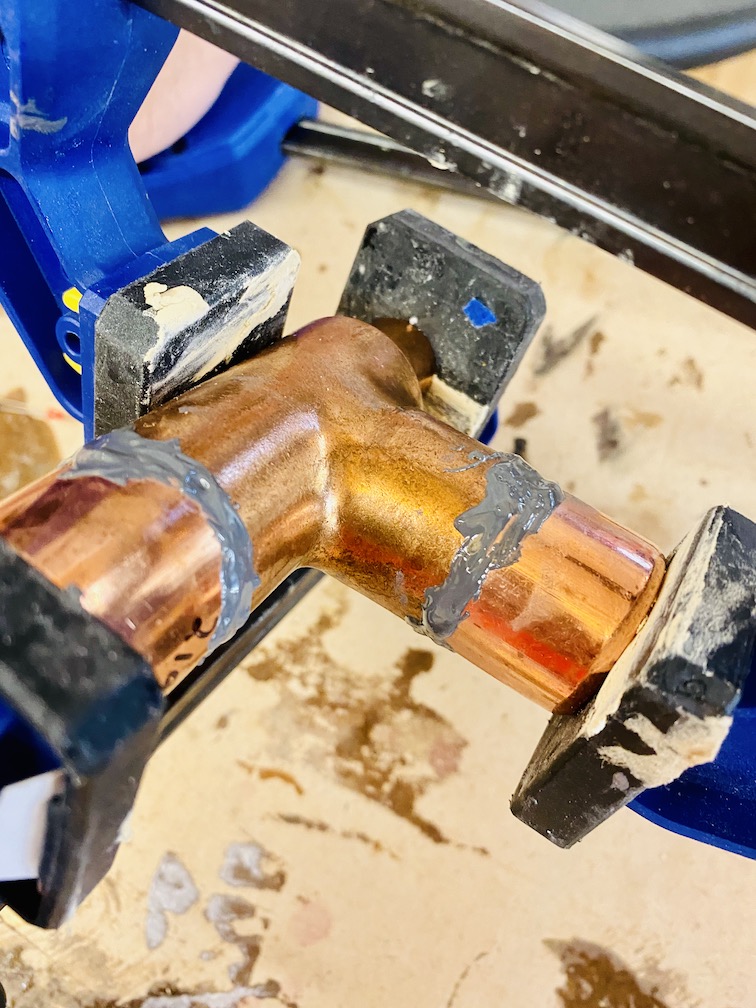
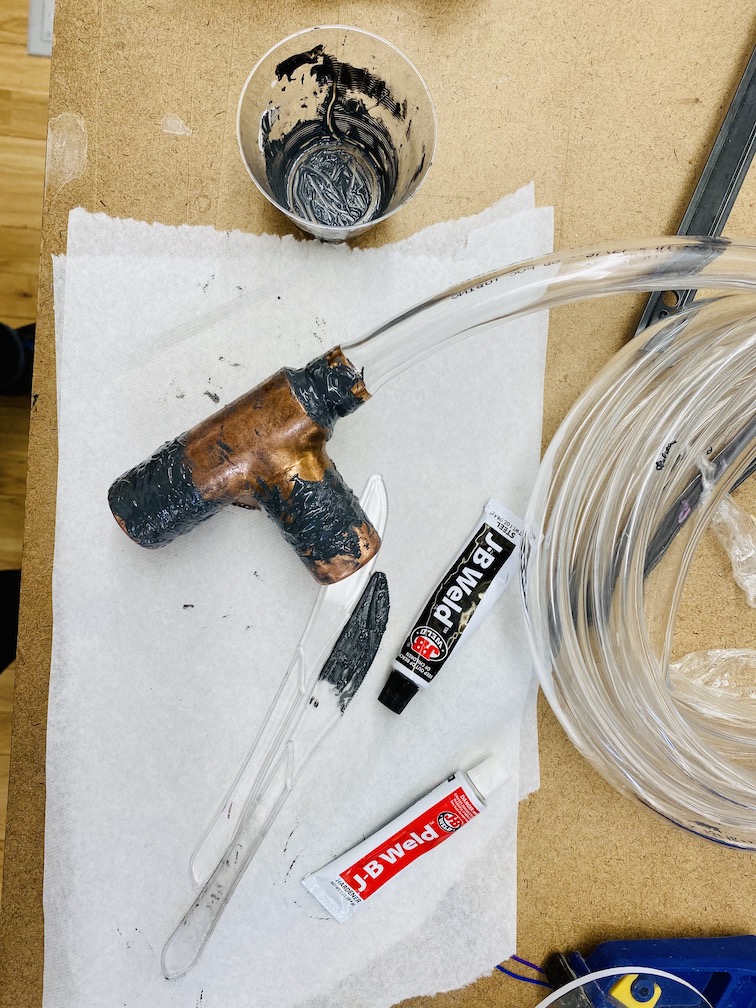
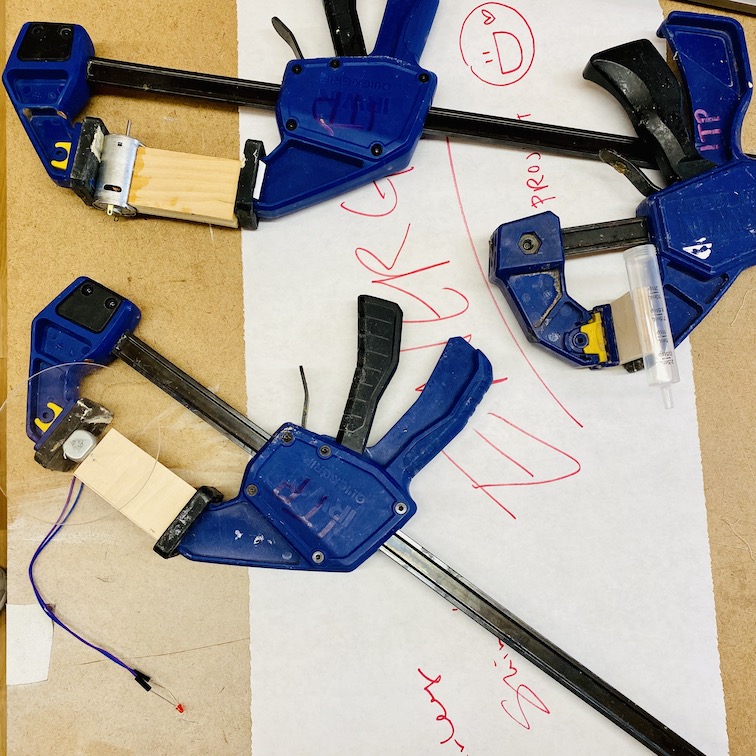
We also acquired epoxy that could withstand up to 500°F heat to join our copper tubing (which are just fittings for plumbing lol) and secure it to silicone tubing (also high temperature safe) that we could attach to the plastic syringe (not high temperature safe) on the other side further away from the candle flame.
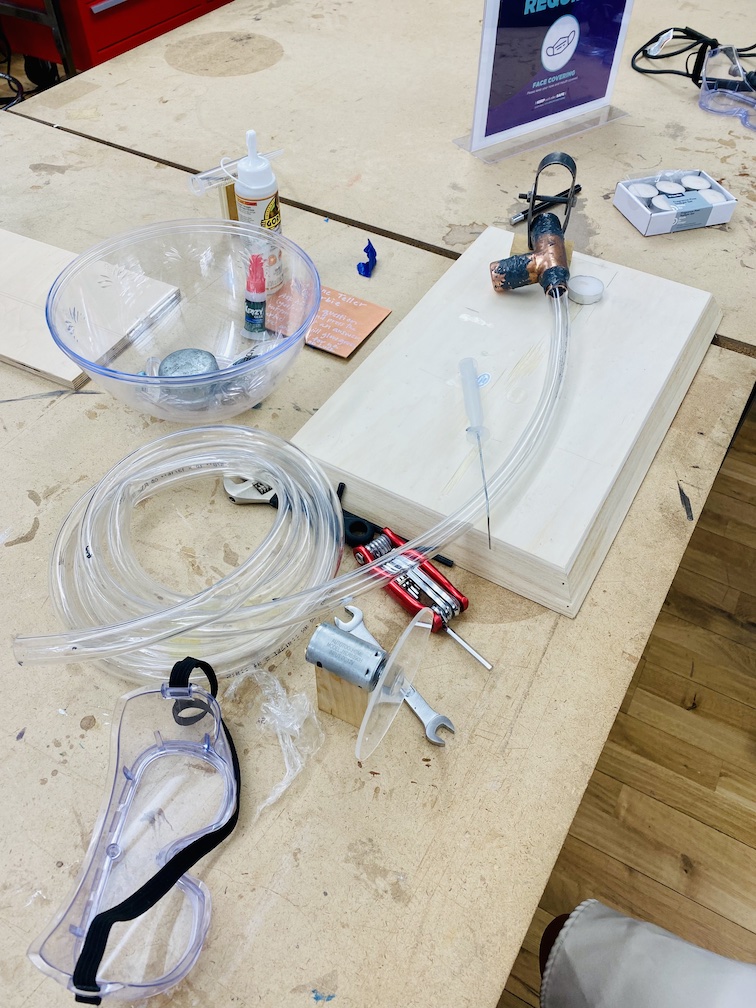
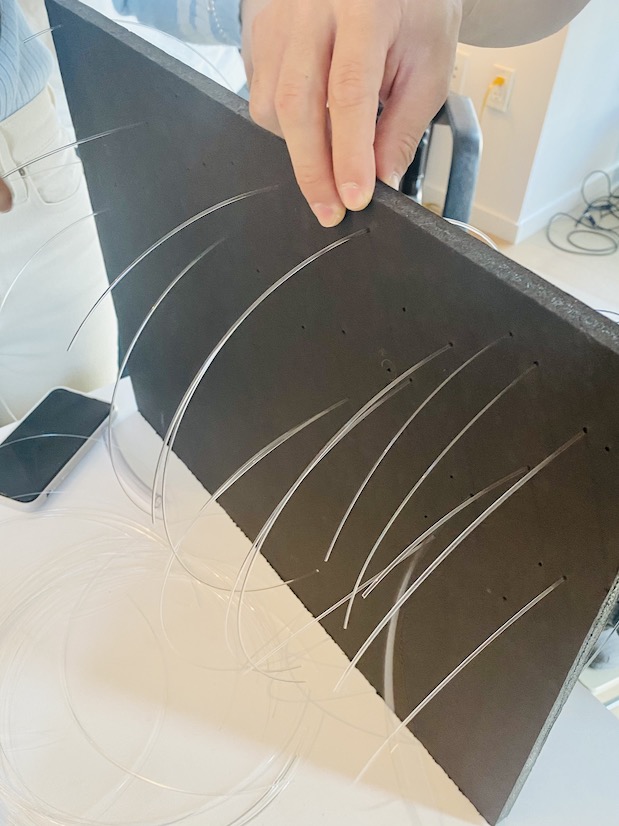
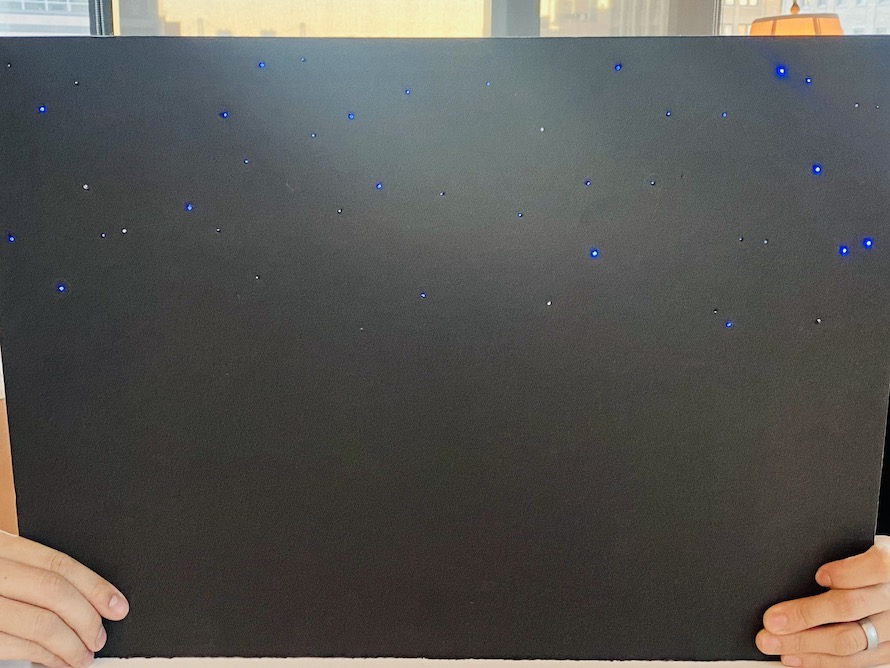
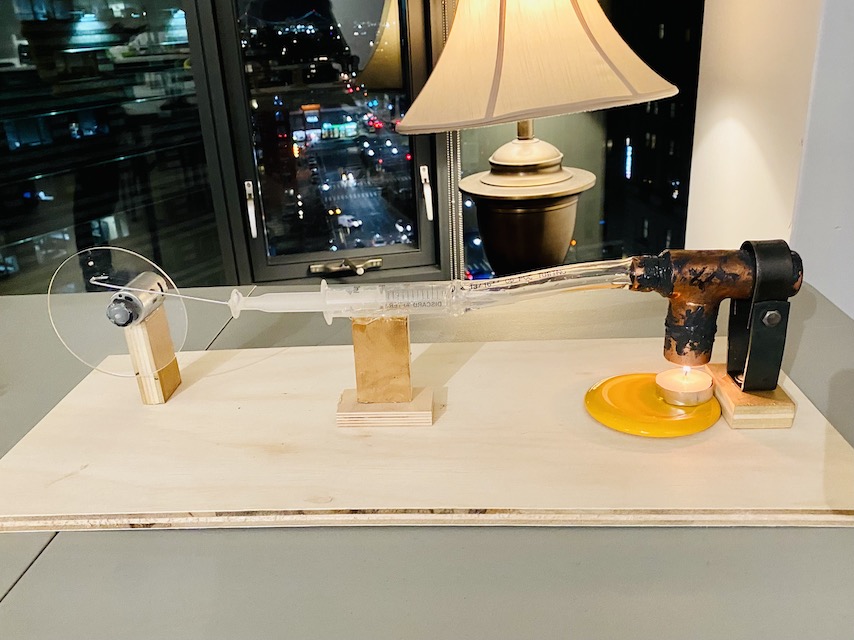
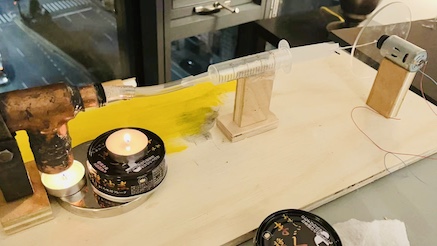
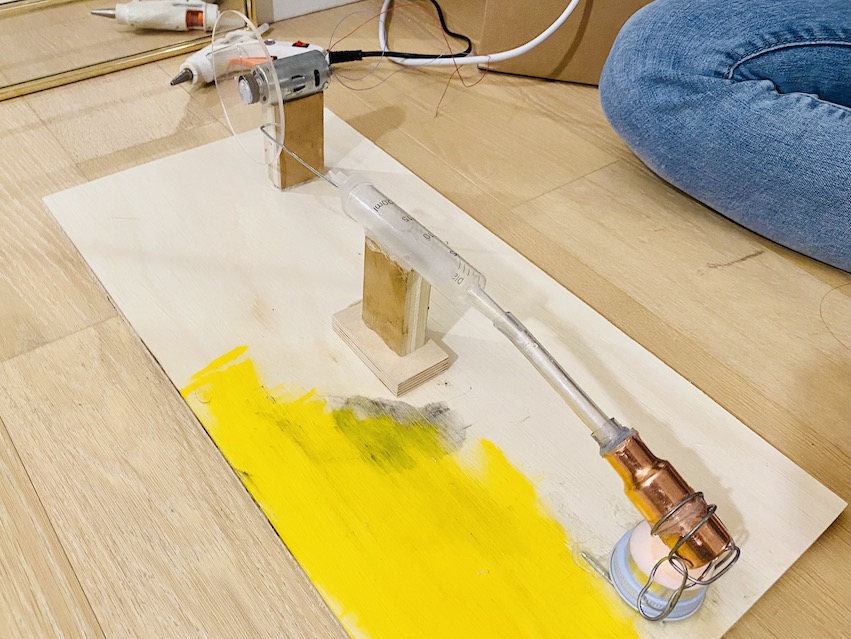
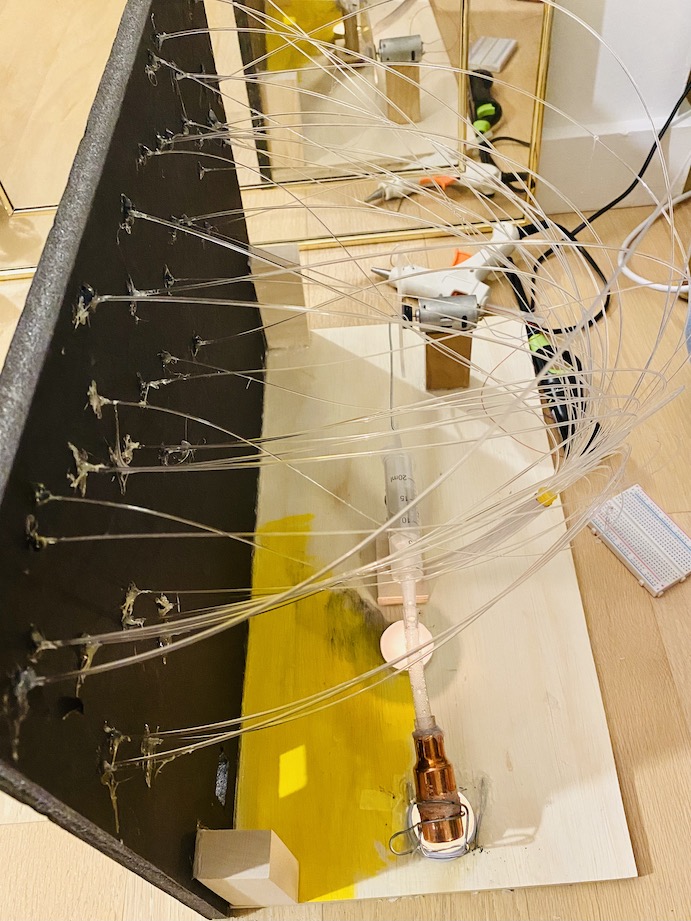
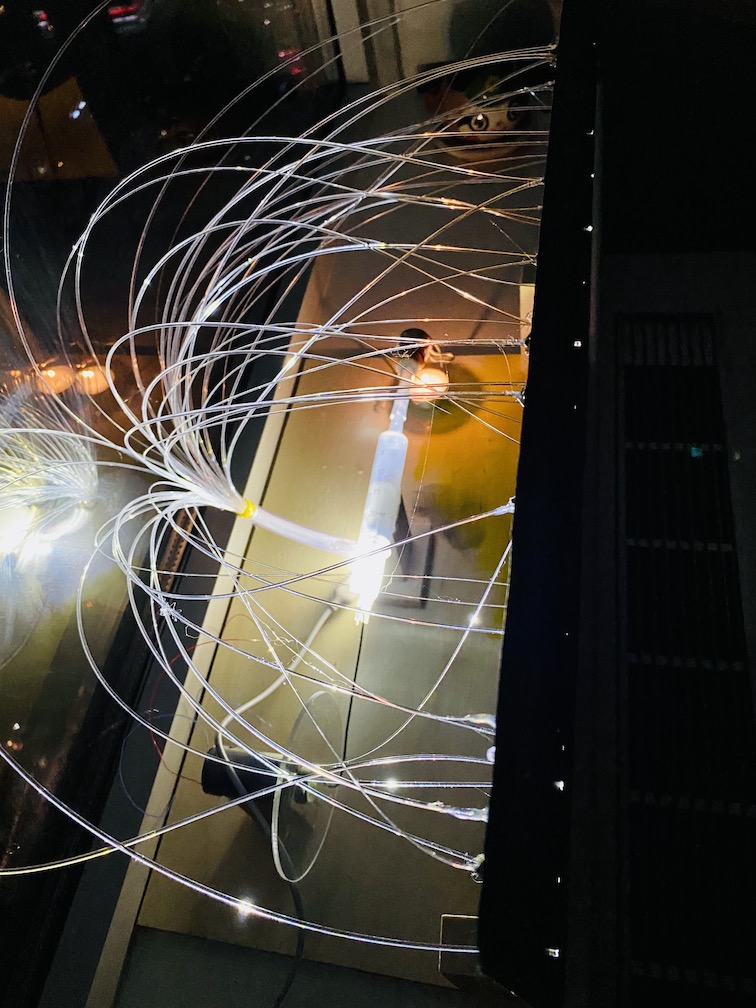
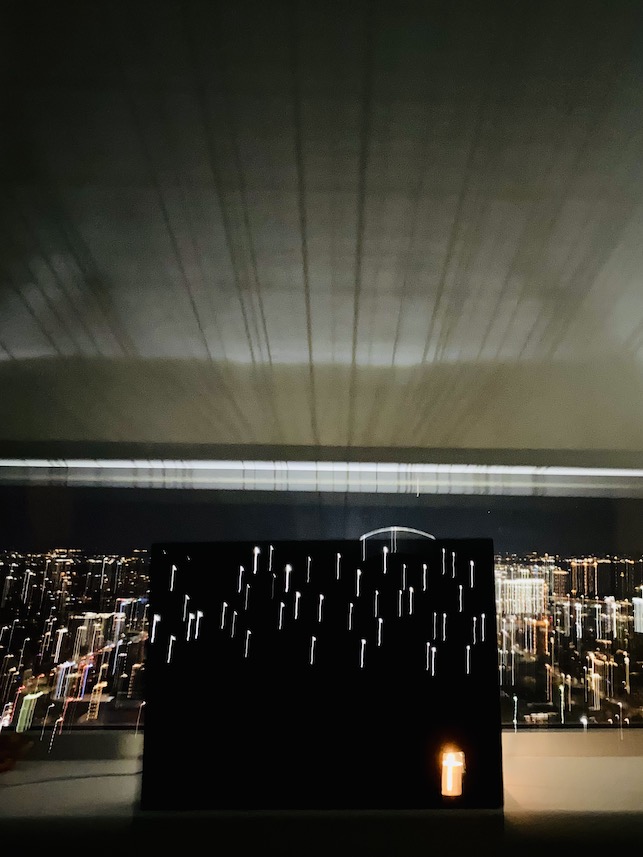
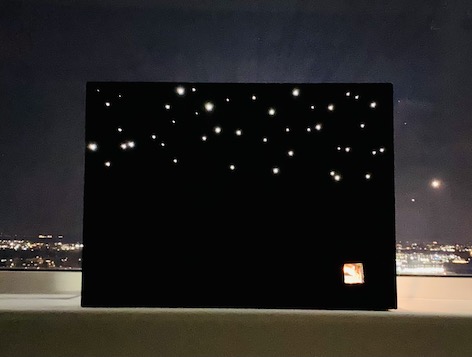
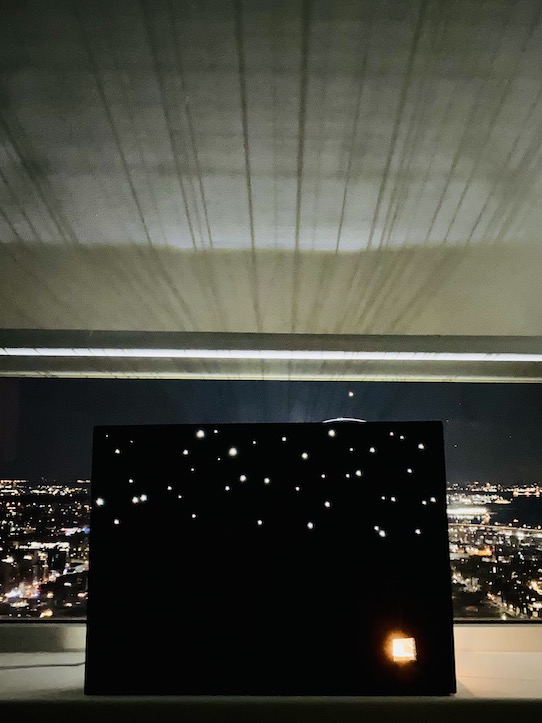